Can You Melt PLA and Reuse It?
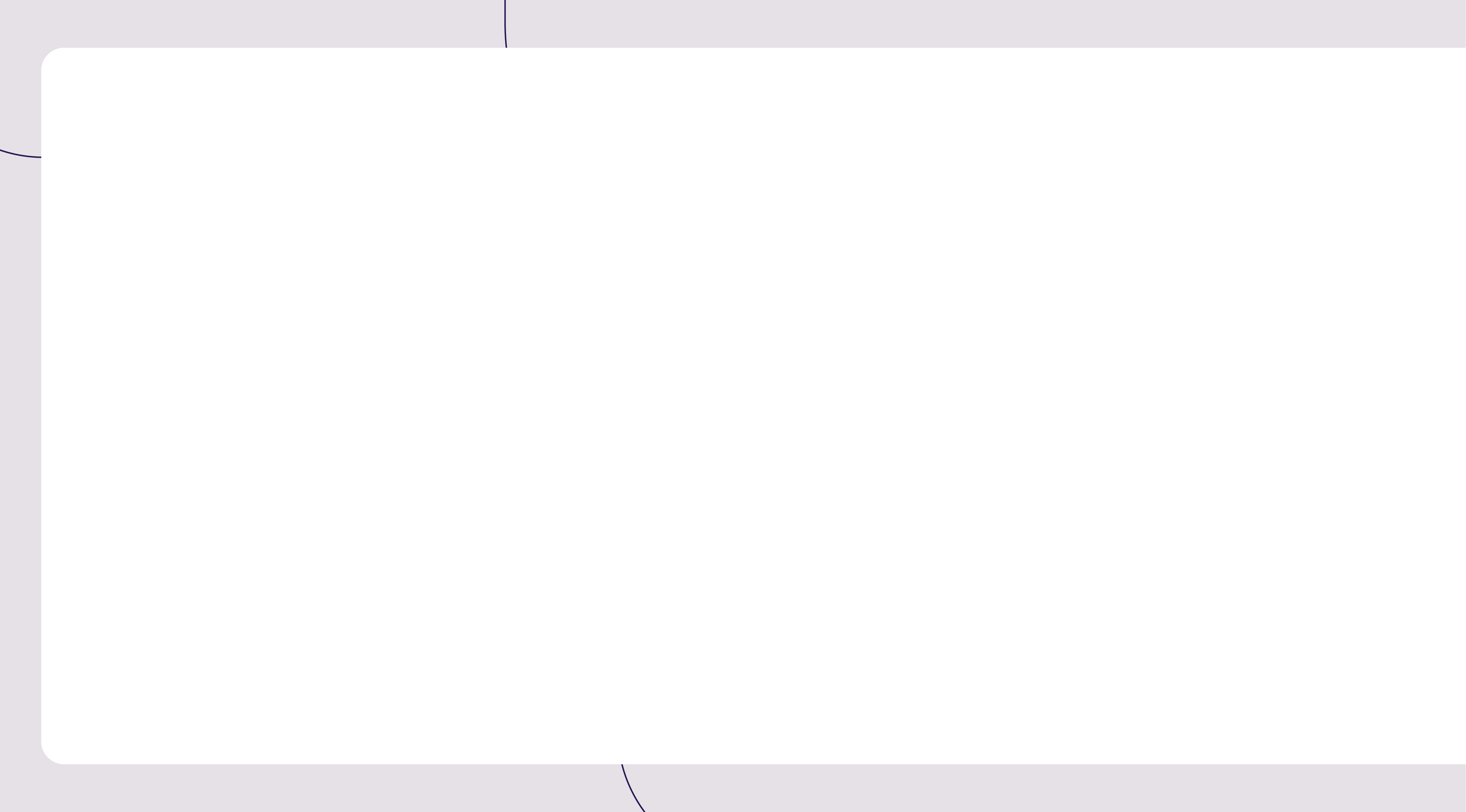

PLA waste accumulates rapidly as you 3D print intensively - such as failed prints, support, and the ends of unused filaments. Can you just melt this material and reuse it? Although PLA can be theoretically melted down, the practical limitations influence quality and usability. This blog explains PLA's nature, ways to reuse it, the problems you'll encounter, and everyday use considerations on your projects.
PLA's Makeup: How Its Properties Affect Reuse
PLA's inherent properties are central to the challenges of reusing it. Let's look at the key material traits that make melting and reforming PLA complex.

PLA is a Thermoplastic
PLA is a thermoplastic. This type of plastic becomes soft and moldable when heated and hardens upon cooling—a cycle that can be repeated. This characteristic is why recycling PLA appears feasible. Two critical temperatures for PLA are:
- Glass Transition Temperature (Tg ): This is around 60-65°C. At this temperature, PLA changes from being hard and brittle to a softer, more rubbery state. It’s not melted yet, but it's much more flexible.
- Melting Temperature (Tm ): This is usually between 150-180°C. The exact temperature can change depending on the specific PLA formula, any colors or other additives used by the manufacturer, and if it’s been heated before. When PLA reaches this temperature, it becomes a thick liquid that can be shaped or pushed through a nozzle, like in a 3D printer.
A Key Problem: Thermal Degradation
Thermal degradation is the primary obstacle in PLA reuse. Each time PLA is melted, its long chemical chains—the source of its strength—can begin to break apart. Heat, oxygen, and moisture accelerate this process. This breakdown leads to several undesirable effects on the material:
- Weaker Material: PLA loses strength and becomes more brittle. Recycled PLA typically breaks more easily than virgin PLA.
- Altered Flow: Degradation changes the melt viscosity (thickness) of PLA. This can hinder consistent extrusion through a nozzle, impacting new filament evenness or mold filling.
- Color Changes: Reheating PLA, particularly if overheated or contaminated, often causes it to darken or yellow. Clear PLA can become cloudy, and colored PLA may turn into a dull, muddled shade.
- Increased Fumes: Degraded PLA can release more Volatile Organic Compounds (VOCs). These fumes can be unpleasant and potentially irritating.
PLA Absorbs Moisture: Why This Is a Problem
PLA is hygroscopic, meaning it readily absorbs airborne moisture. This presents a significant issue for melting. When moist PLA is heated, the water becomes steam. Critically, at melting temperatures, this water can react with PLA via hydrolysis. This chemical reaction further shortens PLA's polymer chains, reducing its strength. It can also cause bubbles and voids in the remelted plastic, resulting in poor print quality or weak spots in manufactured items.
Can You Melt PLA and Reuse It?
Technically, yes, it can be melted and reused. In practice, though, recycling scrap into something of high-quality new filament or useful products is plagued with problems impacting the final product's quality and general feasibility. There are several methods available to attempt this, ranging from simple to equipment-based. Each one has specific uses, benefits, and significant drawbacks.
Option 1: Reshape PLA Scraps with Direct Heat and Simple Molds
This straightforward method for reusing PLA requires minimal specialized equipment.
Process: PLA scraps are heated with a toaster oven (not recommended for food use due to contamination risks), heat gun, or hot plate until softened. Heat-resistant gloves are essential. The softened PLA can then be hand-shaped, pressed into simple molds (e.g., silicone baking molds), or compacted into denser blocks.
Applications: Primarily used for small decorative pieces, basic molds for crafts, or compacting PLA waste.
Advantages: Low cost and simple procedure.
Disadvantages: Difficult temperature control can easily lead to overheating or burning the PLA, producing significant fumes and yielding uneven results. Good ventilation is crucial due to fumes. Unsuitable for creating new 3D printing filament.
Option 2: Extrude New Filament from Cleaned and Shredded PLA Scraps
This approach aims to convert PLA waste directly back into usable 3D printing filament.
Process: This multi-step process involves:
- Thoroughly cleaning scraps to remove dust and oils.
- Shredding or grinding scraps into small, uniform pieces.
- Extensively drying the pieces (often for hours in a filament dryer or controlled oven).
- Feeding dried PLA into a desktop filament extruder, which melts, mixes, and extrudes it as new filament onto a spool.
Primary Goal/Application: To produce new, usable 3D printer filament from PLA scraps.
Advantages: The appeal lies in a 'closed-loop' system, converting waste back into usable material, potentially reducing waste and filament costs over time.
Disadvantages: Significant challenges include:
- High upfront costs for a shredder and filament extruder.
- Time-consuming and labor-intensive process (cleaning, shredding, drying, extruding).
- Difficulty achieving consistent filament diameter and roundness, crucial for print quality, often leading to printer jams or poor prints.
- Inevitable thermal degradation, resulting in weaker filament.
- High risk of contamination (dirt, other plastics) and muddled colors (typically murky brown/gray when mixed).
Option 3: Create Small Solid Objects via Desktop PLA Injection Molding
Processed PLA can also be used in small desktop injection molding machines.
Process: Shredded, thoroughly dried PLA is fed into a small injection molding machine, which heats and injects the molten plastic into a mold under pressure.
Applications: Suitable for producing multiple copies of small, solid parts (e.g., brackets, knobs, casings) where maximum strength is not critical.
Advantages: Can produce fairly consistent parts with good molds and correct settings.
Disadvantages: Desktop injection molders are costly, as is creating quality molds, which also requires skill. Shape complexity is often more limited compared to 3D printing.
Industrial-Scale Recycling of PLA Waste
Despite its bio-based origins, large-scale, dedicated recycling for PLA from 3D prints is uncommon. While some PLA types are certified for industrial composting, this requires access to specialized facilities, and not all PLA qualifies. Standard recycling centers generally find collecting, sorting, and cleaning mixed, often contaminated, PLA 3D prints too complex and costly to be viable.

Major Challenges When Reusing PLA
Melting and reusing PLA typically presents significant and often frustrating problems. These issues nearly always compromise the quality of the final product.
1. Reduced Strength and Increased Brittleness (Thermal Degradation)
As previously noted, thermal degradation is a primary hurdle. Each melt cycle weakens PLA's internal structure. Consequently, reused PLA is almost invariably more brittle and less strong than virgin material, rendering it unsuitable for durable parts, regardless of care taken in a home setup.
2. High Risk of Contamination (Dirt, Colors, Other Plastics)
Recycled PLA is highly susceptible to various forms of contamination:
- Dirt and Oils: Dust, handling dirt, or skin oils can mix with melted PLA, causing imperfections, nozzle clogs, or weak spots in the final product.
- Mixed Colors: Combining different PLA colors typically results in a muddy, unpredictable hue (e.g., brown, dark gray). Achieving bright, clean colors from mixed scraps is nearly impossible.
- Cross-Plastic Contamination: Accidental mixing with other plastics (e.g., ABS, PETG) causes severe issues due to differing melt temperatures and incompatibility. Results include clumps, poor bonding, excessive fumes, and potential equipment damage.
3. Unpredictable Quality and Performance of Recycled Material
Material degradation and contamination combine to produce highly inconsistent recycled PLA.
- Recycled Filament Flaws: Recycled PLA filament frequently exhibits inconsistent diameter, non-circularity, excessive brittleness, or poor melt flow. These flaws directly cause printing problems such as nozzle jams, under- or over-extrusion, and poor layer adhesion.
- Increased Print Failures: The unreliability inherent in recycled PLA often leads to a higher rate of failed prints. This can negate any potential material savings and lead to increased frustration and waste.
4. Increased Fume Emissions and Associated Safety Risks
All PLA heating releases some Volatile Organic Compounds (VOCs). Reheating degraded or contaminated PLA multiple times can worsen the quantity and type of fumes emitted.
- Ventilation Deficiencies: Inadequate ventilation during melting allows VOCs to concentrate, posing potential health risks from inhalation.
- Exposure Hazards: Prolonged or regular exposure to these heightened fume levels, especially without appropriate respiratory protection, can lead to irritation or other health concerns.
5. Significant Investment: Time, Effort, and Financial Cost
The required time, effort, and financial outlay for PLA recycling often outweigh the benefits for most hobbyists.
- Substantial Time Commitment: The entire multi-stage process—cleaning, sorting, shredding, drying, and then carefully extruding or molding—is extremely time-consuming.
- Equipment Investment: Quality shredders, reliable filament extruders, and proper filament dryers represent a significant expense, often exceeding the cost of many spools of new, good-quality PLA. When factoring in the lower quality and higher chance of failed prints associated with recycled PLA, actual cost savings are often minimal or non-existent.
6. Mandatory and Time-Consuming PLA Drying
PLA's hygroscopic nature means it readily absorbs moisture, necessitating thorough and careful drying before any attempt to melt it. Drying introduces another lengthy stage to the reuse process. PLA shreds typically require several hours of drying at a controlled low temperature (around 40−50℃). Failure to dry PLA properly leads to significant problems during melting, such as bubbles and steam, and accelerates material degradation, all of which severely impact the quality of the reused material.
Alternatives to Melting PLA Waste
Instead of going through the difficult process of trying to remelt PLA, there are often more practical and creative things you can do with your PLA scraps and failed prints.
Creative Upcycling:
Failed prints, rafts, and supports can be used in art projects, like mosaics, or as parts of sculptures. Small scraps can be used as interesting filler in resin castings or to create unique textures in other crafts.
Joining PLA Pieces:
You can use a 3D printing pen with PLA filament to "weld" PLA pieces together, fix cracks in prints, or combine smaller parts into bigger ones. Certain glues for plastics, like super glue (cyanoacrylate) used with a plastic primer, or special plastic epoxies, can also work well for sticking PLA parts together.
Specialized Recycling Services (If Available):
These are not common, but some community workshops, makerspaces, or some specialty companies might offer collection and recycling of PLA waste. You can see what is available in your area, but do not hold your breath.
Industrial Composting (for Certified PLA):
If your PLA has the special designation as being suitable for industrial composting (it meets standards like EN 13432 or ASTM D6400) AND you have access to an industrial or municipal compost facility in your area that will accept them, then this is a better environmentally friendly way of getting rid of it. But most PLA will not compost out in a regular household compost bin.
Be Smart About Your PLA Waste!
While it is possible to melt PLA, the truth is that there are great hurdles involved. Material deterioration, quality issues, and the investment of time and equipment generally trump the benefits for the typical hobbyist. Instead of delving into difficult recycling, do your best to reduce your waste by streamlining your prints, creatively upcycle your scraps, or find local composting for certified PLA. Opt for workable solutions for your means over those that promise disappointing results.